Ashley Collimore-Doherty, Ph.D.
Postdoctoral Associate
Global Biomedical Service Program
In June 2015 I had the incredible opportunity to travel to Hong Kong and Heyuan, China as part of the Global Biomedical Service program at the University of Pennsylvania (UPenn). During the two weeks on site, my group was responsible for developing 8 pairs of ankle-foot orthoses (AFOs) for children with cerebral palsy (CP). Below are details my trip and the work we completed.
Learning the Process
On the first day, all the students from the three participating schools met at the Polytechnic University of Hong Kong (PolyU). We were split into teams of 10 people with members from UPenn, Washington University (Wash U) and PolyU. Dr. M. S. Wong, an Associate Professor from PolyU, led a crash course in the orthosis development process and showed us where we would be working. The laboratory at PolyU was incredible and completely dedicated to prosthetics and orthotics.
During the first few days we practiced the AFO making process using one of our team member’s legs as a guide. The PolyU students were familiar with this process and walked us through the plaster mold development, the thermoplastic shaping, cutting, and sanding. After this, we were ready to travel to Heyuan and meet the children we’d be helping.
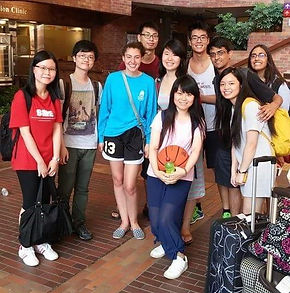.jpg)
My team with members from UPenn, WashU, and PolyU.
First Visit to Heyuan

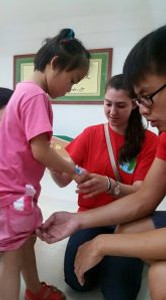
Left: Thermoplastic mold of patient's leg
Right: My teammate and myself conducting an initial evaluation
In Heyuan we set up in a local clinic. By the time we arrived there were already several families waiting, some who had walked days in hopes to get orthoses for their child. Our group had 12 patients assigned to us. With the help of doctors and professors from PolyU, we performed preliminary analyses on the patients muscle strength, gait, and current devices (if they had them). For several children we determined that new orthoses would not be beneficial and instead recommended physical therapy. In the end, the entire team had about 50 pairs of orthoses to make, 8 of which my group was responsible for.
While in the clinic, we used a thermoplastic material to create a mold of each individual child’s legs that we could bring back with us. This allowed us to develop personalized orthoses and improve overall comfort.
Creating the Orthoses
The next step in the process was to fill the mold with plaster, to create a second mold. This new mold would be used for vacuum forming of the final AFO. Once the plaster was set, we performed modifications to the mold including smoothing and shaping. We then heated a solid thermoplastic material and quickly placed and smoothed it over the mold, while vacuuming out the extra air. This process was very delicate and precise as the cooled product would become the final device.
After the plastic was fully cooled, we outlined the final device shape and out the orthosis with a dremel oscillating saw. The device was then trimmed and sanded to create a smooth, comfortable device.
When all the orthoses were completed, we traveled back to Heyuan to deliver the devices. This was truly one of the most incredible moments of my life. We were able to watch children who previously struggled to stand, walk by the end of the day. These orthoses changed the lives of 50 children, but what those children don’t know is that they changed mine as well.

Finished orthoses